Ready for the future
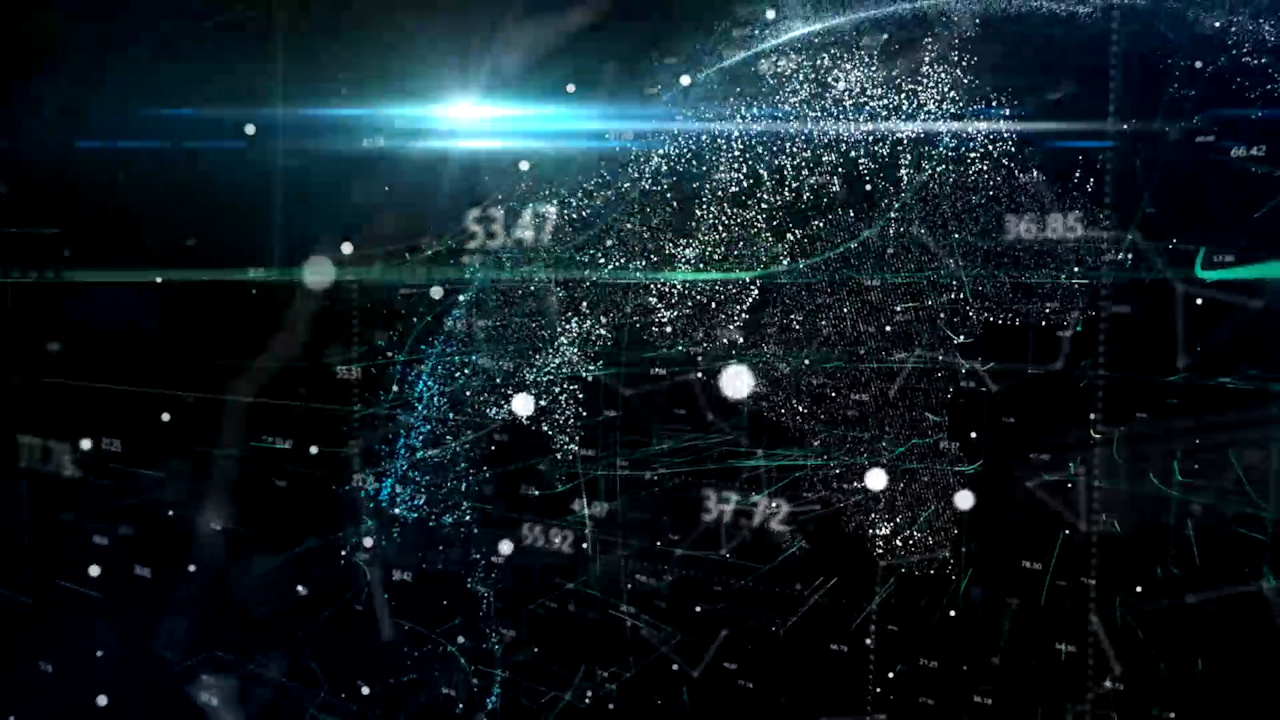
Sandvik is investing in Artificial Intelligence, a venture that is paying off. Customer uptake of predictive maintenance service for mines has increased by 50 percent and a new AI Center for Enablement will further ensure that the Group is ready for the future.
Sandvik has been researching and developing Artificial Intelligence (AI) capabilities for many years but the appointment last year of Rahul Kedia as Head of the Sandvik Artificial Intelligence and Automation Center for Enablement (CFE) says something about the increasing focus that Sandvik now has on the advanced technology.
We are investing significant resources in the development and implementation of AI-based systems.
“Sandvik has been acquiring a lot of industry-specific software companies that are pioneers in AI,” Kedia says. “Organically, we are investing significant resources in the development and implementation of AI-based systems. We are hiring data engineers, data scientists, and other professionals who are working on various AI-based developments. And through the establishment of the AI and Automation Center for Enablement last year, we will enable and expedite the usage and adoption of AI and automation across Sandvik business areas and divisions.”
The CFE works in close collaboration with the various business areas and divisions and the focus is on enabling and supporting them to develop services and products that, through AI and automation, will improve efficiency and productivity for customers, and ultimately generate new revenue streams. “The CFE plays a crucial role by bringing expertise, skills, competence and knowledge sharing from other similar initiatives within Sandvik,” says Kedia.
We use AI to identify when the machine is about to fail. And then we tell the customer to perform certain inspections to fix it before it fails.
One of the first significant AI-enabled services that Sandvik established, Remote Monitoring Service from Sandvik Mining and Rock Solutions is already providing value to customers and increasing revenue streams. Used for predictive maintenance, the service utilizes advanced analytic AI models to identify problems in mine equipment before they occur, thereby enabling mine operators to prevent failures.
“We use AI to identify when the machine is about to fail,” says Esa Mattila, Global Productivity and Reliability Centre Manager, Sandvik Mining and Rock Solutions, who is the driving force behind the Remote Monitoring Service. “And then we tell the customer to perform certain inspections to fix it before it fails. Perhaps we should say prescriptive maintenance. Because as well as predicting what is going to fail, we describe what to do.”
Mattila adds that the groundwork for this service has been laid over many years through connecting machines and sending data to the cloud. “But,” he emphasizes, “the ability to understand the data through AI models on such a big scale, and accurately give the customer quick visibility about what will happen and what needs to be done, is revolutionary.”
When the machines break down less they can be utilized more and they consume fewer spare parts.
This visibility enables customers to significantly improve efficiency and cut costs. By analyzing the improvements that the service made for one customer, Mattila determined that the utilization of machines increased by 15 percent and the costs of using the equipment decreased by 20 percent. “That is a massive improvement,” he says. “And that is because they had visibility of what is happening and visibility to understand what to do next. This resulted in the machines breaking down less often. And when the machines break down less they can be utilized more and they consume fewer spare parts.”
Customer uptake of the Remote Monitoring Service increased by 50 percent last year. “And we see that it is ramping up further,” says Mattila. “Customers understand the value of how we can improve their operations through data.”
Identification of new opportunities
As well as predicting equipment failures, Kedia points out that AI can be used in many other ways to improve customer efficiency and productivity. “AI can be used to optimize production processes, improve energy efficiency and improve supply chain management,” he says. “It can also help customers identify new opportunities for growth and innovation.”
And of course, AI can be used to increasingly automate operations. “The more we store data, the more AI can be used to automate things,” says Matilla.
Being at the forefront of AI is already helping some of our customers improve their productivity.
The CFE has in fact evolved out of work to develop Robotics Process Automation; automating simple tasks that were repetitive in nature and had a pre-defined algorithm. “We subsequently added new technologies like Intelligent document processing and conversational AI,” says Kedia. Currently, the CFE is focused on, among other things, moving from more conventional automation to intelligent process automation and end-to-end business process automation.
“This is being enabled through design thinking and rapid process scan workshops with businesses to understand their top challenges,” Kedia explains. “We are currently supporting a plant in the US to evaluate more than 500 processes to understand whether it is possible to automate part of the process or the entire process.”
Safer working environment
While automated processes may cause concern for some people regarding the future of jobs, Matilla points out that AI-enabled services make the working environment safer because there is better understanding all the time of what is happening. “It reduces the probability of catastrophic hazards,” he says. “And with AI we can automate the processes so that we can identify in real time what is happening next and make sure that the resources and tools are available for people to perform their duties more efficiently. It ultimately makes processes safer, more sustainable and more efficient.”
The CFE is also working on tasks that include establishing an agile framework and Sandvik common processes and procedures when it comes to AI and automation.
“Being at the forefront of AI is already helping some of our customers improve their productivity,” says Kedia. “And it will help Sandvik make a variety of advancements for its customers in the future. By increasingly opening up several opportunities, including better decision-making, cost reductions, improved safety, supply chain optimization and personalized customer service, AI will also help us improve the quality of our products and services, thereby creating new revenue streams and improve our competitiveness.”
Remote Monitoring Service
- Development began in 2018 by establishing the environment, making the data available, analyzing the data, understanding it and then selecting the right algorithms to scale the insights.
- The data that the AI uses to make predictions is gathered in the cloud from connected Sandvik mining equipment being used at customer’s mines.
- First made available to paying customers in 2020.
- Over 700 machines are currently being monitored in over 50 mines.
Image and speech recognition
Sandvik is looking at use cases for AI-enabled tools such as image and speech recognition.
- Image recognition could, for example, be used to help automated mining equipment recognize boulders in tunnels or help machine-cutting tools make exact copies of components.
- Speech recognition could be used to make background systems more interactive with human operators.
Are you looking for a new opportunity? When you become one of us, you will develop and thrive in an inclusive and learning culture that welcomes you to be your authentic self.